Step 1 - Defining the boundary of the scan area
To define the boundary, select <Teach>. You will be prompted to
capture points along the perimeter of the scan area. When you have captured
3 or more data points, press the Terminate key, <F5>. The scan tool
will calculate the diameter and position then populates the cells in the
Radial Scan Parameters Group with the results.
Step 2 Establishing the grid density
Ensure the Grid Distance value has the proper data point density value
you want to scan. This Grid Distance is the distance between columns and
rows.
Step 3 Building the Motion Path
Build the initial motion map through the use of <Build Path>. The
Scan Tool will report the total number of points that will be captured based
on the current settings.
Adjustments can now be made to the motion path. These adjustments include
changing the Grid Distance and the building of exclusion zones.
To change the point density, enter a new value in Grid Distance and press
<Build Path> again. This will discard the existing motion path and
compute a new one based on the changed Grid Distance value. NOTE: Making
a change to the Grid Distance and then computing a new motion path will
delete any existing exclusion zones.
To review how the scan tools create rows and columns, please read
Understanding
the Data Cloud Structure.
Step 4 Exclusion Zones
One very important feature of the Scan Tool is the ability to eliminate
areas within the defined scan boundaries. A common example might be a hole
through the surface you are scanning. There are two types of Exclusion Zones
available.
Diameter Exclusion Zone:
This tool works well to define exclusion zones around holes. Building a
zone starts by pressing the <Teach Dia> button which prompts you to
capture data points around the area to exclude.
When you have captured sufficient points, press the terminate key, <F5>. The scan tool will calculate the exclude area and determine the
number of data points that will be excluded. Press <Remove> to
complete the exclusion.
 |
Exclusion Zone Confirmation
Message |
4-Point Boundary Exclusion Zone:
This exclusion zone shape has the same characteristics as the boundary
definitions in Step 1. To build the zone, press <Teach 4Pt> and then capture
the 4 data points.
After the last point was captured, The scan tool will calculate the
exclude area and determine the number of data points that will be excluded.
Press <Remove> to complete the exclusion.
The surface may require several exclusion zones to be defined. You can
create as many exclusion zones as necessary to build a proper scan.
 |
Exclusion Zone Confirmation
Message |
Step 5 Establish a Clipping Plane
If you require your scan boundary to extend beyond the surface, setting a
Clipping Plane will help clear unwanted data points. Here we have an example
of a scan that was done on a fan blade assembly. The boundary extended
beyond the fan and included the surface plate the fan was positioned on.
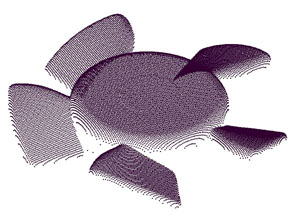 |
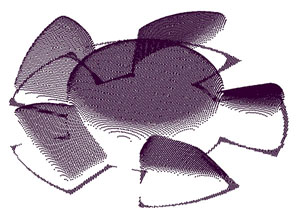 |
Clipping Plane Active |
Clipping Plane NOT Active |
The added data points on the surface plate would interfere with spline
operations and result in poor surface generation by CAD systems.
To establish a Clipping Plane, press <Clipping Plane>. You will
then capture one data point on the surface that you want excluded from the
final data cloud. During the scan process, each captured point will be
evaluated and if it has a Z value equal to, or below, the Clipping Plane, if
it does it will be discarded.
Step 6 Use Z Clearance Height
The motion required to perform surface following by the scan tool
involves the comparing the Z component of the current data point to the
previous data:
Zdelta = Zcurrent pt Zprevious pt
That difference is then added to the next data point to be scanned.
Znext pt = Zcurrent pt + Zdelta
This is the simple explanation of contour following tool, there are other
filters and controls in place to enhance the surface following capabilities.
The Z Clearance Height setting takes over the Z component adjustment
formula and builds the motion path by using a constant Z height. Using the
fan blade as an example, the step from the surface plate to the upper edge
of the blade was over 1.25. The CMM would approach this large step and
crash.
Using the Z Clearance Height, you would set the height sufficient to
clear the entire fan, then every data point would retract to that height
before proceeding to the next data point assuring full clearance for all
steps.
Step 7 Stand Off and Over Travel
From the drop down menu, choose [DCC Settings→Standoff Distance].
The standoff distance should be sufficient to clear any vertical steps on
the surface. Under [DCC Settings→Over Travel Distance], should
be sufficient to drop off a vertical step and still locate the data point.
Step 8 Execute
To begin the scanning operation, press <Execute>. The system will
prompt you to position the CMM over the first data point in the motion path.
When you have the CMM in that position, press the <IP> button on the
joystick controller. Depending upon whether the Z Clearance Height is in
effect will determine how the scan operation will take place.
Related Procedures:
Select Scan Method,
4-Point Boundary Scan,
Line Scan,
GeoTracer,
Cardinal Splines,
Export
Tool
|